The construction industry is constantly evolving, and 3D printing is emerging as one of the most revolutionary technologies. By using robotic printers to build structures layer by layer, this innovative method is transforming the way homes, offices, and infrastructure are designed and constructed.
But how does 3D printing in construction work, and what impact does it have on the industry? Let’s explore its process, benefits, challenges, and real-world applications.
How Does 3D Printing in Construction Work?
3D printing in construction, also known as additive manufacturing, involves depositing material layer by layer to form walls, floors, and other building components. Instead of using traditional bricks, concrete, or wood, this method employs specialized concrete mixtures, polymers, or recycled materials to create durable structures.
Step-by-Step Process of 3D Printing in Construction
- Digital Design: Engineers and architects create a 3D model of the building using software like BIM (Building Information Modeling).
- Material Preparation: The printing material, typically a quick-drying concrete mix or polymer, is prepared for extrusion.
- Printing Begins: A large robotic arm or gantry system moves along a pre-programmed path, extruding material layer by layer to create walls and structures.
- Structural Reinforcement: Depending on the project, steel reinforcements, insulation, or finishing materials may be added manually.
- Final Assembly: Once the printing process is complete, additional elements like windows, doors, and roofing are installed.
This process eliminates the need for traditional bricklaying, formwork, and excessive manual labor, making construction faster and more efficient.
Benefits of 3D Printing in Construction
1. Faster Construction Time
Traditional construction projects take months or even years to complete. With 3D printing, a house can be built in as little as 24 to 48 hours.
- Example: In China, a company printed 10 houses in 24 hours using a large-scale 3D printer.
- Disaster Relief: 3D-printed homes are being used to provide quick shelter for people affected by natural disasters.
2. Reduced Material Waste
Traditional construction generates tons of waste, including excess concrete, wood, and steel. 3D printing uses only the exact amount of material needed, reducing waste by up to 60%.
- Sustainable Materials: Many 3D printing projects use recycled plastic or eco-friendly cement, further reducing environmental impact.
3. Cost Savings
3D printing can cut construction costs by up to 50% due to:
- Lower labor costs (fewer workers needed).
- Less material waste.
- Shorter project timelines (faster completion reduces financing costs).
4. Design Flexibility
Unlike traditional methods, where shapes and curves are difficult to achieve, 3D printing allows for complex architectural designs that would otherwise be too expensive or time-consuming.
- Custom shapes and intricate details can be created with ease.
- Organic and futuristic designs become more accessible.
5. Sustainability and Energy Efficiency
Since 3D-printed structures require fewer resources and generate less waste, they contribute to a more sustainable construction industry. Some projects even use biodegradable or locally sourced materials to further reduce their carbon footprint.
Challenges of 3D Printing in Construction
1. High Initial Investment
While long-term savings are significant, the upfront cost of acquiring 3D printing technology, software, and skilled professionals can be high.
- Large-scale printers cost millions of dollars.
- Training is required for architects, engineers, and workers to adapt to the technology.
2. Material Limitations
Current 3D printing materials, primarily concrete-based mixtures, have limitations in:
- Strength and durability (compared to traditional reinforced concrete).
- Compatibility with plumbing and electrical systems.
3. Building Regulations and Approval
Many countries lack clear regulations for 3D-printed structures, leading to challenges in:
- Obtaining permits for construction.
- Ensuring safety and compliance with building codes.
As the technology advances, governments and regulatory bodies will need to update policies to support 3D-printed buildings.
Real-World Applications of 3D Printing in Construction
1. Residential Housing
Countries like China, the Netherlands, and the United States are using 3D printing to construct affordable and sustainable homes.
- ICON, a U.S. company, is building 3D-printed houses for low-income families.
- Europe’s first 3D-printed home was completed in the Netherlands.
2. Commercial and Industrial Buildings
Companies are experimenting with 3D printing for offices, retail stores, and warehouses.
- Dubai Municipality built the world’s largest 3D-printed office in just 17 days.
3. Infrastructure Projects
3D printing is being used to create bridges, pedestrian walkways, and urban structures.
- The world’s first 3D-printed concrete bridge was built in Amsterdam.
- China has printed pedestrian bridges using recycled concrete.
4. Space Construction
NASA and the European Space Agency (ESA) are exploring 3D printing for lunar and Mars habitats, using regolith (moon dust) as a building material.
The Future of 3D Printing in Construction
As technology advances, 3D printing will become more affordable and widely adopted in the construction industry. We can expect:
- Stronger and more diverse materials, including composite and carbon fiber-based options.
- AI-driven printing processes to further improve precision and efficiency.
- Regulatory frameworks to evolve, making large-scale adoption easier.
With its potential to reduce costs, increase efficiency, and promote sustainability, 3D printing is set to revolutionize the way we build cities, homes, and infrastructure.
Would you live in a 3D-printed home? The future of construction is being built—one layer at a time!
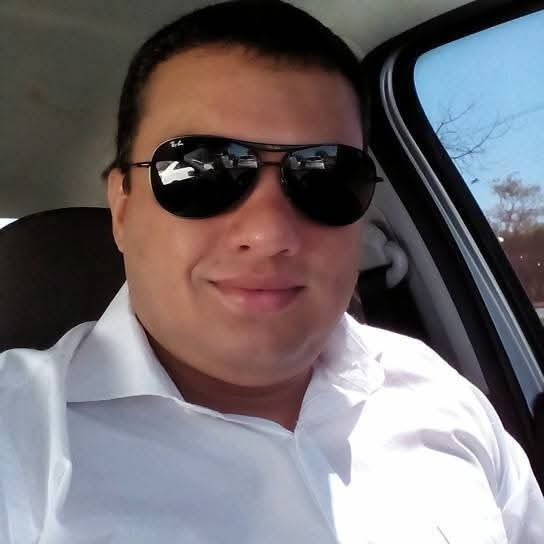