The construction industry is rapidly shifting towards off-site construction, an innovative method that improves efficiency, reduces waste, and lowers costs. By manufacturing building components in a controlled environment and assembling them on-site, this approach eliminates many of the challenges faced in traditional construction.
But how does off-site construction work, and why is it gaining popularity? Let’s explore its process, advantages, challenges, and real-world applications.
What is Off-Site Construction?
Off-site construction refers to the design, fabrication, and assembly of building components in a factory or controlled facility before they are transported to the final construction site. These components can include walls, floors, roofs, and even entire rooms or modules.
Off-site construction includes:
- Prefabrication: Individual components are manufactured off-site and assembled on-site.
- Modular Construction: Entire sections of a building (such as apartment units) are built, finished, and transported for quick assembly.
By moving much of the construction process away from the site, companies can speed up projects, reduce waste, and ensure higher quality standards.
How Does Off-Site Construction Work?
- Design & Planning: The project is designed using Building Information Modeling (BIM) to optimize components for off-site production.
- Factory Manufacturing: Walls, floors, and modules are built under controlled conditions, improving precision and quality.
- Transportation: Completed elements are delivered to the construction site for installation.
- On-Site Assembly: The components are connected, stacked, and secured, drastically reducing the need for extensive on-site labor.
Since most of the work is completed off-site, construction schedules become more predictable and efficient.
Advantages of Off-Site Construction
1. Faster Project Completion
Off-site construction can reduce building timelines by 30-50%. Since factory production and site preparation happen simultaneously, projects move faster compared to traditional methods.
- Example: A traditional hotel project may take two years, while an off-site modular hotel can be completed in under one year.
- Disaster Relief: Prefabricated housing can be rapidly deployed after natural disasters.
2. Cost Savings
By streamlining production and minimizing waste, off-site construction can lead to significant cost reductions.
- Less material waste (precise factory cutting reduces excess).
- Lower labor costs (fewer workers needed on-site).
- Faster completion times mean lower financing and operational costs.
3. Improved Quality Control
Since building components are made in a controlled factory environment, they are:
- More precise and durable than on-site-built components.
- Less affected by weather conditions, reducing errors and material damage.
- Subjected to strict quality inspections, ensuring compliance with industry standards.
4. Sustainability and Waste Reduction
Off-site construction is an eco-friendly alternative to traditional methods.
- Up to 90% less construction waste.
- Lower carbon footprint due to reduced transportation needs.
- Recyclable and energy-efficient materials are commonly used.
5. Safer Work Environment
Factory-based construction reduces on-site risks, such as:
- Accidents from working at heights or handling heavy machinery.
- Exposure to extreme weather conditions.
- Physical strain from repetitive manual labor.
Challenges of Off-Site Construction
1. High Initial Investment
- Setting up off-site manufacturing facilities requires significant capital.
- Companies need to invest in automation, robotics, and skilled labor.
2. Transportation & Logistics
- Large prefabricated components require specialized transportation.
- Some locations have road access limitations that make deliveries difficult.
3. Design Limitations
- Customization is limited compared to traditional methods.
- Pre-planning is crucial, as changes mid-project can be costly.
Where is Off-Site Construction Being Used?
1. Residential Housing
Countries like Sweden, Japan, and the U.S. are using off-site construction for mass-produced, affordable housing.
2. Hotels & Commercial Buildings
- Marriott and Hilton are expanding using modular hotels.
- Google and Amazon are integrating prefabricated office spaces.
3. Healthcare Facilities
- Prefabricated COVID-19 hospitals were built in weeks during the pandemic.
- Off-site construction is ideal for rapidly expanding hospitals and clinics.
4. Educational Buildings
- Schools and universities use modular classrooms to quickly expand capacity.
5. Infrastructure Projects
- Bridges, tunnels, and railway stations are increasingly built using prefabrication.
The Future of Off-Site Construction
With advancements in automation, AI, and robotics, off-site construction will continue to grow in popularity. Expect:
- More eco-friendly materials to improve sustainability.
- AI-powered automation to enhance precision and reduce costs.
- Wider adoption across residential, commercial, and infrastructure projects.
As cities grow and construction demand increases, off-site methods will become the standard, offering a faster, cheaper, and more sustainable alternative to traditional construction.
Would you consider off-site construction for your next project?
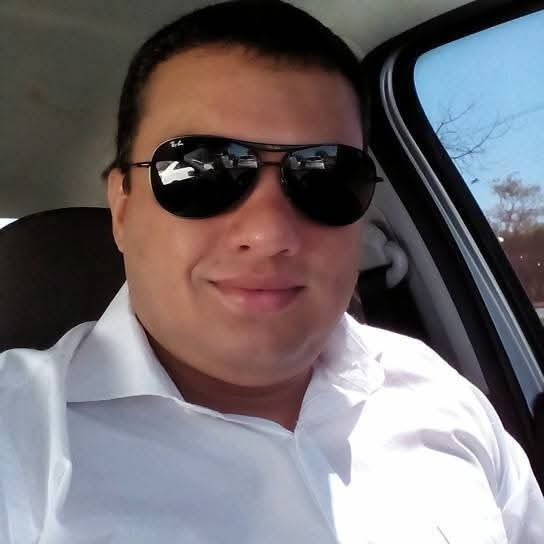